CIP System: Cleaning in Place
CIP system is required to clean the equipments in place. The CIP process is generally customised as per the client requirements, ensuring optimal cleaning and hygiene standards for each application.
Flexible CIP System Options
CIP system has wide ranging applications. The system can be built with storage tanks and also tankless system can be provided to suit the client requirements.
This flexibility makes it suitable for a wide range of industries, including pharmaceuticals, biotech, dairy, and food & beverage.
SIP System: Sterilizing in Place
SIP system are required to sterilise plants and equipments in place. The SIP process are designed to ensure maintenance of sterilisation temperature and pressure during the entire sterilisation cycle, ensuring effective sterilization without compromising equipment integrity.
Combo Plants for CIP & SIP
For optimal efficiency, a combo plant can be built to integrate both CIP and SIP systems in a single unit. This combined solution streamlines the cleaning and sterilization processes, reducing downtime and improving operational efficiency.
Applications
Both CIP and SIP systems have extensive applications in various industries, such as:
- Pharma & Biotech Industry: Ensuring high levels of cleanliness and sterilization in sensitive manufacturing processes.
- Dairy: Maintaining hygiene standards in dairy processing equipment.
- Food & Beverage: Guaranteeing food safety and hygiene during production and processing.
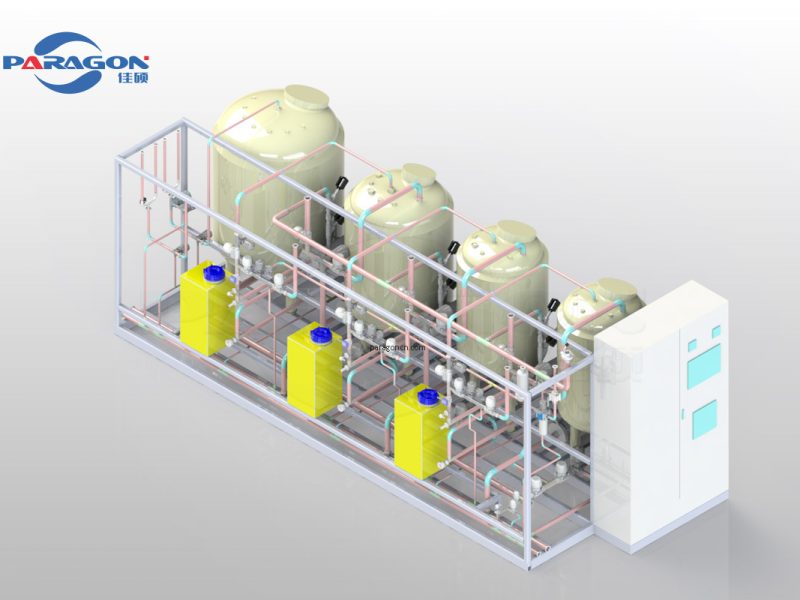
Features
- CIP / SIP System is provided with instruments to monitor parameters like temperature, conductivity, pH and TOC
- The system is designed and constructed to comply with ASME BPE & cGMP.
- CIP / SIP systems are integrated with high grade instrumentation and PLC based automation to control and monitor the operations with highest level of integrity yet user interface remains simple and easy to understand. If required SCADA system can also be incorporated.
- Various options can be provided to achieve sanitisation temperature, like jacketed tank, tank with electric heaters and Double Tube Sheet type Heat exchangers can be provided
- CIP system are designed to make sure it passes riboflavin test
- Inter connecting piping is designed for minimum dead leg criterion of < 1.5 D
- Fully drainable design by proper arrangement of equipments and by maintaining the minimum slope of 1:100 for inter connecting piping
- All piping weld joints are orbital welded using High Purity (99.99%) Argon Gas and can be inspected by boroscopy machine.
- GAMP 5 sentence
- Complete set of documentation and certificates to ensure compliance with regulatory authority